May 29,2024
Raw Material Preparation: PVC (polyvinyl chloride) resin is mixed with various additives to create a compound with the desired properties. Additives can include plasticizers, stabilizers, impact modifiers, UV inhibitors, and colorants. These additives enhance the material's flexibility, durability, and resistance to environmental factors.
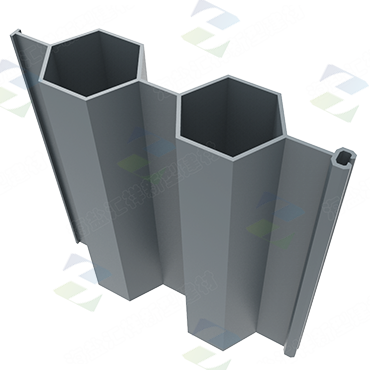
Compounding: The PVC compound is thoroughly mixed to ensure uniform distribution of additives and a consistent material composition. This is usually done in a high-speed mixer or compounder.
Pelletization: The compounded PVC material is formed into small pellets or granules. This makes it easier to handle, transport, and feed into the extrusion process.
Extrusion Process:
Hopper Feeding: The PVC pellets are fed into the hopper of an extruder, which is a machine that consists of a rotating screw within a heated barrel.
Heating and Melting: As the pellets move through the barrel, the screw rotates, applying heat and pressure to melt the PVC pellets. The melted PVC forms a homogenous molten mass.
Die Design and Calibration:
Die Design: The die is a specially shaped tool that defines the cross-sectional profile of the PVC sheet pile. It includes features like interlocking mechanisms, reinforcement structures, and any other design elements required for the specific application.
Calibration: The die is carefully calibrated to ensure the accurate dimensions and characteristics of the final product.
Extrusion and Forming:
Extrusion: The molten PVC is forced through the calibrated die using the rotating screw. The die shapes the material into the desired profile, which includes the interlocking sections and any other design features.
Cooling: After exiting the die, the formed PVC sheet pile is rapidly cooled to solidify its shape. This can be achieved using water cooling tanks or air cooling systems.
Cutting and Sizing:
Cutting: The continuous extruded PVC profile is cut into individual sheet pile sections of the desired length.
Sizing: The cut sections are further sized and trimmed to achieve precise dimensions and ensure uniformity.
Quality Control:
Throughout the process, quality control checks are conducted to monitor factors such as temperature, pressure, material composition, profile accuracy, and surface finish.
Testing might include measuring dimensions, inspecting interlocking mechanisms, and assessing the material's structural integrity.
Surface Treatment (Optional):
Some PVC sheet piles might undergo surface treatment processes to enhance features such as texture or UV resistance.
Packaging and Distribution:
The finished PVC sheet piles are packaged and prepared for shipping to construction sites or suppliers.
Proper packaging helps protect the sheet piles from damage during transportation and storage.